Combustion Test Facility
Mitsubishi Power maintains world-class combustion test facilities, which it utilizes to achieve even more sophisticated combustion technologies that form the basis of boiler performance, including lower nitrogen oxide (NOx) emissions, less unburnt fuel, and a reduced excess air ratio. We are particularly focused on enhancing the following two functions of our combustion test facilities to support cutting-edge technological development.
- Functions to accurately recreate in-flame combustion phenomena in actual boilers
- Functions to evaluate flow and combustion to a high level of accuracy through precision measurement instrumentation
In addition, our testing facilities support a wide range of fuels used in power plant boilers, such as the following.
- Bituminous coal, subbituminous coal, lignite and anthracite
- Solid and gaseous biomass fuels
- Oil-based fuels including residue oil, petroleum coke and crude oil
- Vacuum residue (VR) and solvent de-asphalting (SDA) pitch
We also enhance functions to evaluate the combustibility of cheap, low-grade fuels, reduce fuel costs, improve utilization and contribute to reduce environmental load.
Combustion Test Furnace, Photography of Actual Flames and Sample Results from Numerical Calculations
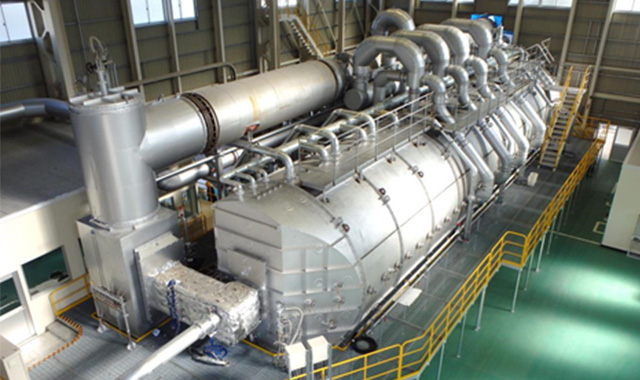
Combustion Test Facility (4t/Hour)
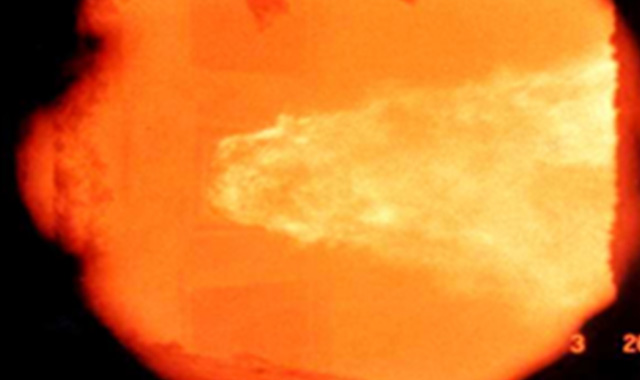
Photo of Flame During Combustion Testing

Pulverized coal
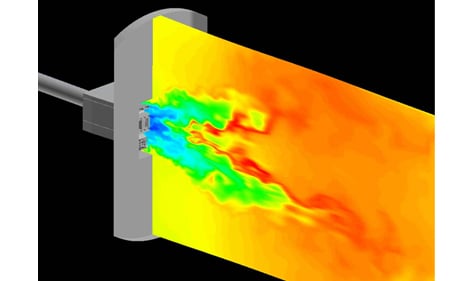
Numerical Analysis Results (In-burner Temperature Distribution)
High-functionality Combustion Test Facility (Coordination Between Numerical Analysis and Combustion Testing)
- Combustion test results are fed back into the system to develop more sophisticated numerical analysis
- High-precision numerical analysis is used to improve the reliability of boiler performance evaluation
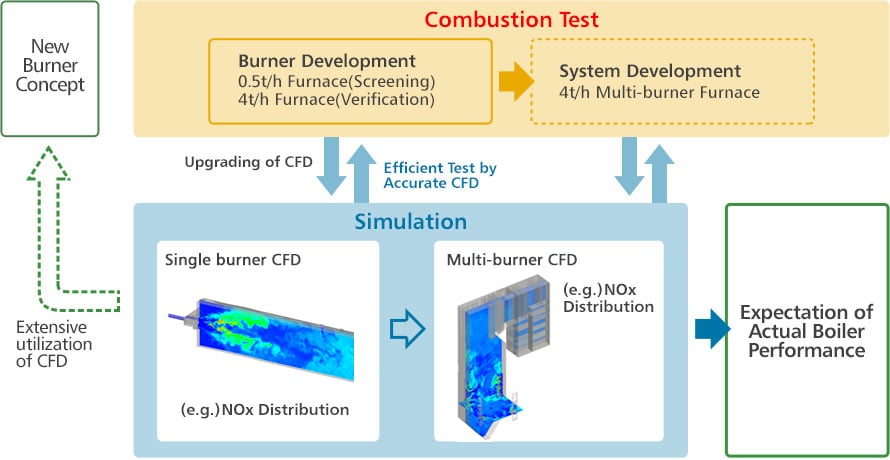
Main Feature of Combustion Testing Equipment
Uses
Developing low NOx and high-efficiency burners (for swirl combustion and opposing combustion)
Main Fuels
- Coals (bituminous coal, subbituminous coal, lignite and anthracite)
- Oils (residue oil, vacuum residue (VR), solvent de-asphalting (SDA) pitch, oil coke, etc.)
- Biomass (solid, gaseous)
Main Equipment
- 4t/h combustion test furnace: φ4.4m × 20m
- 0.5t/h combustion test furnace: φ2.2m × 10m
- Pulverized coal supply: 2t/h pulverizer, 52m3× 2 silos, high-temperature oil tank, etc.
Sophisticated Measurement Instrumentation for High-Reliability Design and High-Precision Numerical Analysis
Combustion zone | Details of measurement advancements | Measurement Instrumentation |
---|---|---|
Ignition zone |
|
|
Reductive combustion zone | In-furnace distribution measurement
|
|
Oxidized combustion zone |
|
|
Products
- GTCC
- Steam Power
- IGCC
- Geothermal
-
Gas Turbines
- Product Lineup
- Comparative Performance
-
Technical Information
- Gas Turbines for Mechanical Drive Applications
- Cutting-Edge Elemental Technology Producing 1600°C Class J Gas Turbines
- Development of High-Efficiency Gas Turbine Applying 1600°C Class J Technology
- Combustor Technologies Supporting Stable Operation
- Overview and Verification Status of T-Point 2 Demonstration Facility
- Comprehensive Efforts from Development to Manufacturing
- Summary of Orders
- Development History
- Product Selection Assistant (Middle & small Class)
- Aero-derivative Gas Turbines
- Steam Turbines
- Boilers
- Air Quality Control Systems (AQCS)
- Generators
-
Control Systems
- What is DIASYS?
- DIASYS Netmation
-
DIASYS Optional Products
- IR-S Infrared Flame Detector
- Net IR-S Infrared Flame Detector
- Rail Mounting Net IR-S
- Boiler Tube Leak Detector
- Shaft Vibration Analyzer
- Simulator
- Advanced Combustion Pressure Fluctuation Monitoring System (A-CPFM) / Combustion Pressure Fluctuation Monitoring System (CPFM)
- Multi-Coal Fired Boiler Optimum Control
- FXtoLS Adapter
- Fuel Cells
- Catalogue
- HIACS Series
- Technical Report