M501G Series
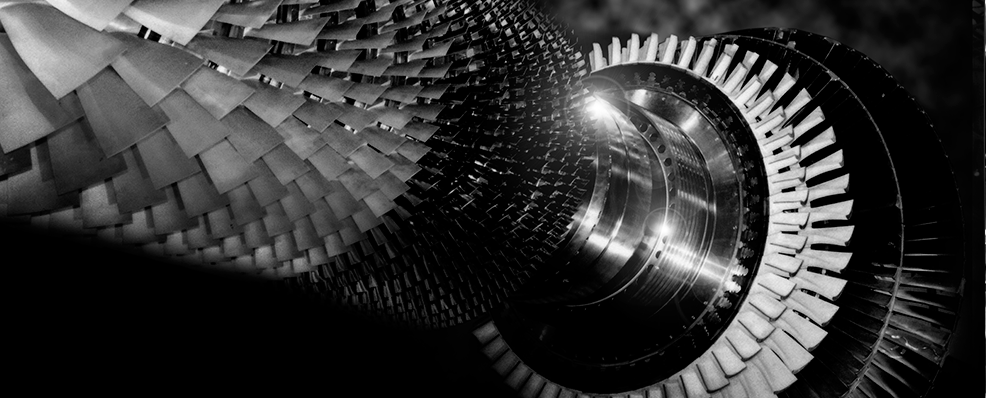
-
Standalone Gas Turbine Output
280 MW class
-
Combined Cycle Output
430MW/860MW/1,280MW class
-
Combined Cycle Efficiency
More than 60%
High-performance large-capacity gas turbines for 60 Hz power generation
In February 1997, the first unit of the 1,500°C Class M501G gas turbine came into commercial operation. This series features the use of steam for cooling combustors. The GAC Series, which is the current mainstay model, adopts the latest air-cooled combustors in place of conventional steam-cooled combustors. It uses compressor discharge air for cooling combustors to add operational flexibility by eliminating the need for steam for cooling from the bottoming cycle.
Overall Design
The gas turbine unit is based on the basic structure adopted in the early 1970s that has accumulated a track record of at least 50 years. Its main features are as follows:
- A compressor shaft end drive reduces the effect of thermal expansion on alignment
- A rotor with simple single-shaft two-bearing support
- A rotor structure has bolt-connected discs with the torque pins in the compressor section and CURVIC couplings in the turbine section to ensure stable torque transmission
- An axial flow exhaust structure advantageous in combined cycle plant layouts
- Horizontally split casings that facilitate field removal of the blades with the rotor in place
Compressor
Axial flow compressors designed with advanced airfoil design technologies are introduced. They feature large capacity, high efficiency and a high pressure ratio. Variable inlet guide vanes ensure operational stability at the start-up and enhanced performance at partial load in combined cycle operation.
Combustor
A premixing low NOx combustor is a steam-cooled type, composed of one pilot burner and eight main burners that surround it. The combustor has an air bypass mechanism that enables fuel-air ratio regulation in the combustion region.
Incorporating air-cooled combustors, the GAC series adds operational flexibility by eliminating any need for steam cooling from the bottoming cycle.
Turbine
Four-stage axial flow turbines in a three-dimensional aerodynamic design are adopted. The vanes at the first three stages are air-cooled. Among these, those at the first two stages adopt directionally solidified (DS) materials with thermal barrier coating (TBC). Despite the rise in temperature, application of advanced cooling technologies and the TBC helps to maintain the metal temperature of turbine blades at the level of conventional gas turbines.
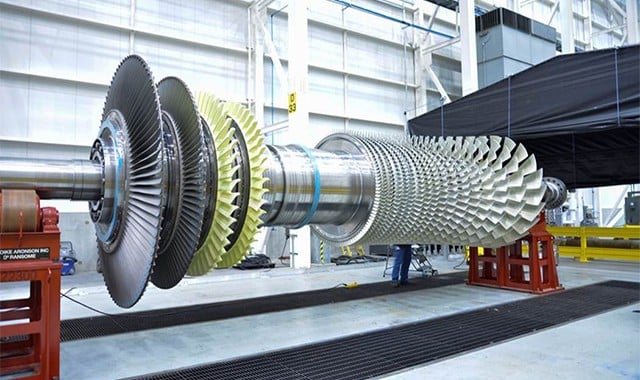
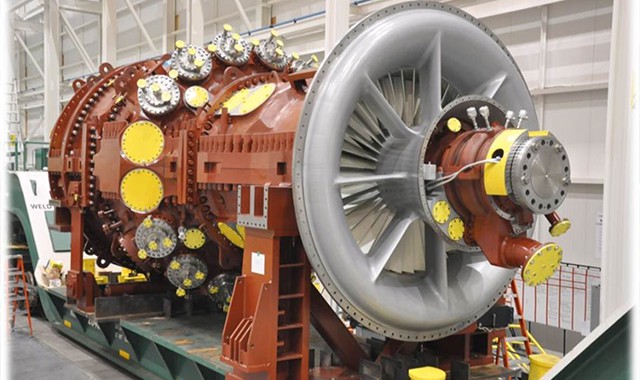
Configuration
M501GAC | ||
---|---|---|
Compressor | Number of Stages | 17 |
Combustor | Number of Cans | 16 |
Cooling Method | Air Cooled | |
Turbine | Number of Stages | 4 |
Rotor | Number of Rotors | 1 |
Output Shaft | Cold End | |
Rated Speed | 3,600 rpm | |
Gas Turbine | Approx. L × W × H | 12.9 × 5.1 × 5.5 m |
Approx. Weight | 295 ton |
Simple Cycle Performance
M501GAC | ||
---|---|---|
Frequency | 60 Hz | |
ISO Base Rating | 283 MW | |
Efficiency | 40.0 %LHV | |
LHV Heat Rate | 9,000 kJ/kWh | |
8,531 Btu/kWh | ||
Exhaust Flow | 618 kg/s | |
1,364 lb/s | ||
Exhaust Temperature | 617 °C | |
1,143 °F | ||
Exhaust Emission | NOx | 15ppm@15%O2 |
CO | 9 ppm@15%O2 | |
Turn Down Load | 50 % | |
Ramp Rate | 18 MW/min | |
Starting Time | 30 minutes |
Combined Cycle Performance
M501GAC | ||
---|---|---|
1 on 1 | Plant Output | 427 MW |
Plant Efficiency | 60.5 %LHV | |
2 on 1 | Plant Output | 856 MW |
Plant Efficiency | 60.7 %LHV |
Performance Correction Curves
-
Effects of Compressor Inlet Temperature on Gas Turbine Performance (Typical)
-
Effects of Barometric Pressure on Gas Turbine Performance (Typical)
Typical Plant Layout - 1 on 1 configuration, single-shaft
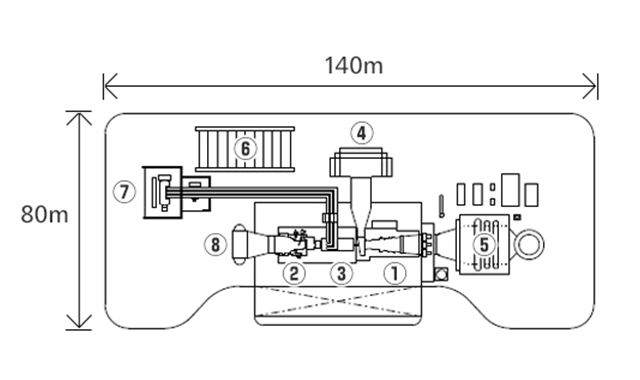
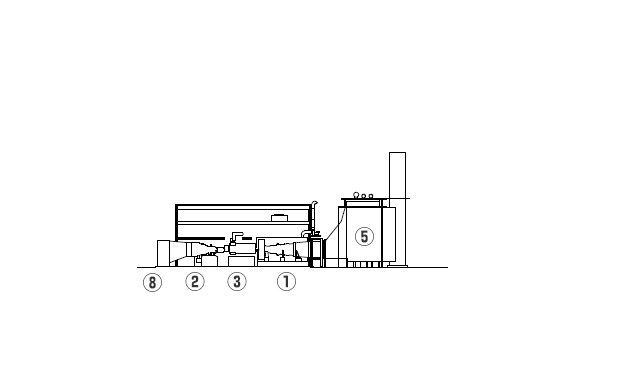
- Gas Turbines
- Steam Turbines
- Generators
- Inlet Air Filter
- Heat Recovery Steam Generator (HRSG)
- Electrical / Control Package
- Main Transformer
- Condenser
Typical Plant Layout - 2 on 1 configuration
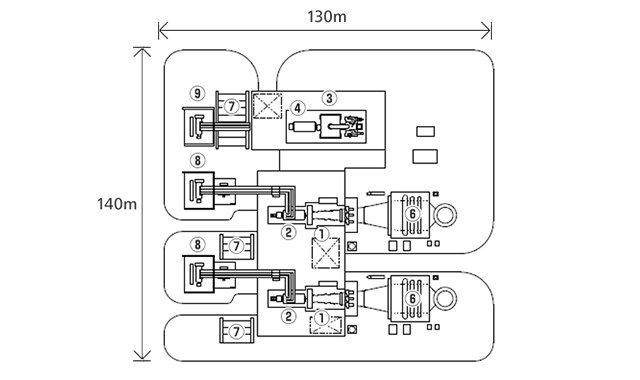
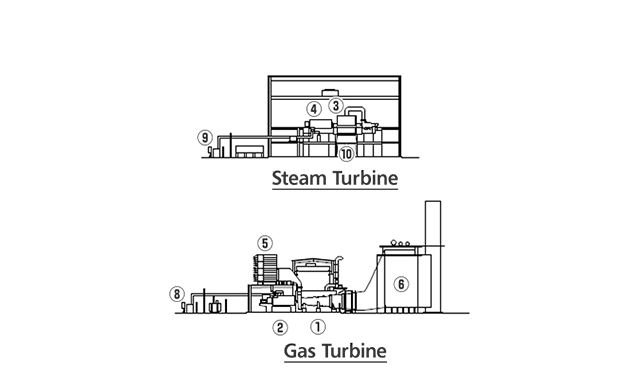
- Gas Turbines
- GT Generator
- Steam Turbines
- ST Generator
- Inlet Air Filter
- Heat Recovery Steam Generator (HRSG)
- Electrical / Control Package
- GT Main Transformer
- ST Main Transformer
- Condenser
Delivery Records Example
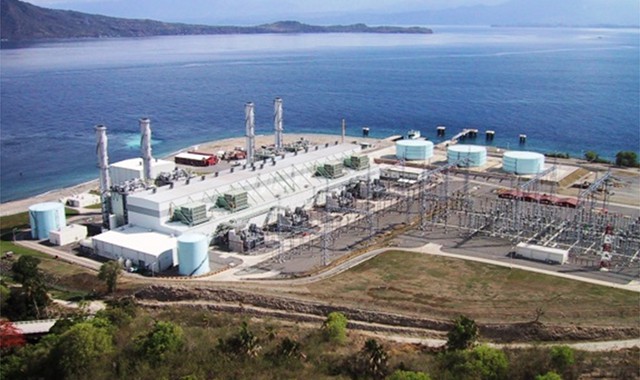
KEILCO Ilijan (The Philippines)
1,250 MW, 4 x M501G
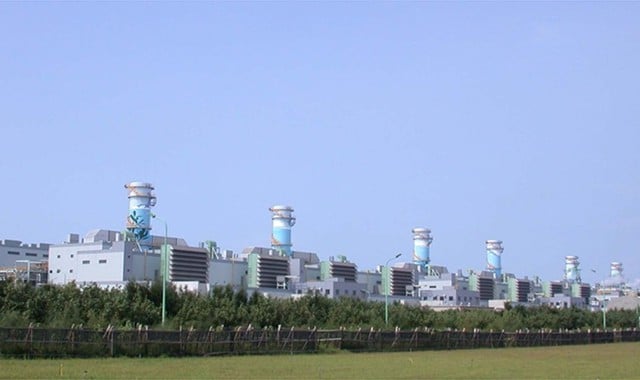
Datan Power Plant, Taiwan Power Company (Taiwan)
4,200 MW, 8 x M501G & 6 x M501F
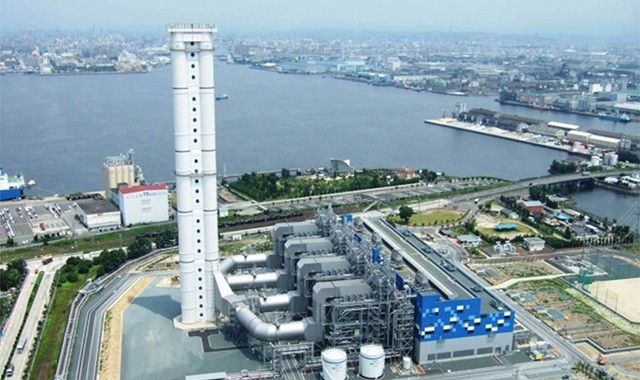
Shin-Nagoya Thermal Power Station Group 8, Chubu Electric Power Co., Inc. (Japan)
1,600 MW, 4 x M501G
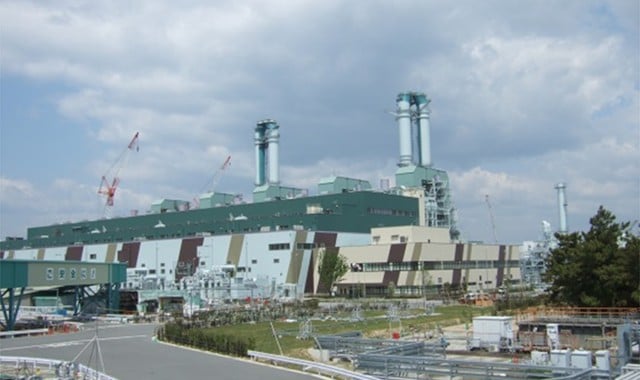
Sakaiko Power Station, the Kansai Electric Power Co., Inc. (Japan) (Photo courtesy of the Kansai Electric Power Co., Inc.)
2,000 MW, 5 x M501G
Order Results Example
Number of units x Series | Year of start of operation | Plant specifications | |
---|---|---|---|
Carty Generating Station, Portland General Electric (PGE) (USA) | 1 × M501GAC | 2016 | Combined cycle |
Wildcat Point Generating Facility, Old Dominion Electric Cooperative (ODEC) (USA) | 2 × M501GAC | 2017 | Combined cycle |
Toyama Shinko Thermal Power Station, Hokuriku Electric Power Company (Japan) | 1 × M501GAC | 2018 | Combined cycle |
Middletown Energy Center, NTE Energy (USA) | 1 × M501GAC | 2018 | Combined cycle |
Kings Mountain Energy Center, NTE Energy (USA) | 1 × M501GAC | 2018 | Combined cycle |
Products
- GTCC
- Steam Power
- IGCC
- Geothermal
-
Gas Turbines
- Product Lineup
- Comparative Performance
-
Technical Information
- Gas Turbines for Mechanical Drive Applications
- Cutting-Edge Elemental Technology Producing 1600°C Class J Gas Turbines
- Development of High-Efficiency Gas Turbine Applying 1600°C Class J Technology
- Combustor Technologies Supporting Stable Operation
- Overview and Verification Status of T-Point 2 Demonstration Facility
- Comprehensive Efforts from Development to Manufacturing
- Summary of Orders
- Development History
- Product Selection Assistant (Middle & small Class)
- Aero-derivative Gas Turbines
- Steam Turbines
- Boilers
- Air Quality Control Systems (AQCS)
- Generators
-
Control Systems
- What is DIASYS?
- DIASYS Netmation
-
DIASYS Optional Products
- IR-S Infrared Flame Detector
- Net IR-S Infrared Flame Detector
- Rail Mounting Net IR-S
- Boiler Tube Leak Detector
- Shaft Vibration Analyzer
- Simulator
- Advanced Combustion Pressure Fluctuation Monitoring System (A-CPFM) / Combustion Pressure Fluctuation Monitoring System (CPFM)
- Multi-Coal Fired Boiler Optimum Control
- FXtoLS Adapter
- Fuel Cells
- Catalogue
- HIACS Series
- Technical Report